Ultrasonic Lubrication Monitoring
Maximize performance and optimize bearing life with precision ultrasound assisted greasing
Ultrasonic technology can be used to detect increased bearing friction through acoustic emissions.
✓ Applications, demo and pricing
Insufficient lubrication is one of the leading causes for bearing damage, so proper lubrication is essential to reduce friction, minimize wear and prevent costly equipment failures.
- Condition-based lubrication
- Avoid wear due to incorrect lubrication
- Increase system availability
- Prevent unplanned downtime
Cost savings through proper lubrication
Efficient lubrication is critical to keeping your machinery running smoothly and preventing costly downtime. Traditional lubrication schedules often lead to over- or under-lubrication, causing unnecessary wear and failures. With our advanced lubrication monitoring solution, you can achieve condition-based lubrication and damage detection with ease - saving time, reducing costs, and improving overall equipment health.
✓ Applications, demo and pricing
Contact us to start reducing bearing failures and extending the lifespan of your machinery!
Advantages
- Earliest Detection with Ultrasound: Identify bearing damage at its earliest stages using our cutting-edge ultrasonic technology.
- Right Lubricant, Right Amount, Right Interval: Apply the exact amount of grease, precisely when and where it’s needed - eliminating guessing.
- 2-in-1 Device: Benefit from a unique solution that combines lubrication management and damage recognition in a single device.
- Broadband Sensor: Unmatched sensitivity for precise measurements at all bearings speeds.
- Easy Handling and Reporting: Simplify your maintenance processes with intuitive apps and Asset Tree Management for fast execution and reporting.
Save cost and increase bearing life with ultrasound condition monitoring
Ensure your bearings are lubricated perfectly - not too much, not too little.
The lubrication process
- Create a route for the next lubrication job using an existing asset tree or create a new one using the AssetExpert module in the DataSuite PC software. You can define the type and color code of grease, as well as measurement setup and alarm levels in the asset details.
- Export the route to the SONAPHONE and follow the AssetExpert app's instructions for the route-based work process.
- Start inspecting the bearings with our dedicated GreaseExpert app, guiding you through the measurement process. Our SONAPHONE together with our BS40 broadband sensor allows easy and accurate measurements to determine the lubrication needs of each bearing.
- Grease the bearings as needed according to the information provided by the app and document the results. Immediate status feedback through a traffic light system makes it easy to know if and how much grease needs to be applied to the bearing.
- Import the results back into your DataSuite. After automatic synchronization, you can view the results in the AssetExpert module. Using the DataReport module, you can then easily create a report and save it for trend analysis.
Upgrade your lubrication process with our ultrasonic solutions
Why ultrasound?
Detecting damage at the earliest possible stage is the key to an effective maintenance process and equipment cost savings.
The acoustics of a bearing are the first parameter to change. Heat development, vibrations and audible noises only occur at an advanced stage. At this point, the bearing is already showing signs of damage and may need to be replaced quickly to avoid downtime.
Lubrication and damage recognition in one device
Detecting a change in acoustics in the ultrasonic range not only allows the early detection of damage, but also enables the proper lubrication of bearings, making ultrasound the perfect technology to prevent your bearings from failing.
The SONAPHONE® ultrasonic testing device, combined with our optimized PC-Software DataSuite, and our BS40 broadband sensor with high sensitivity at all rotational speeds, allows for a fast and reliable maintenance process.
Downloads
Do you have any questions?
Feel free to contact us! We will be happy to help you.
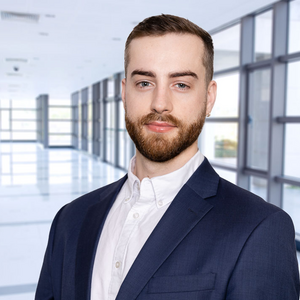