Bearing Inspection
Recognize Bearing Damage Early and Optimize Bearing Lubrication with Ultrasonic Testing Devices
Ultrasonic testing devices allow the earliest possible detection of damage to roller and ball bearings. Regular inspections of bearings in industrial plants are essential in preventive maintenance.
The failure of individual bearings can interrupt and cause unplanned downtime of entire processes. This leads to production losses and generates immense costs.
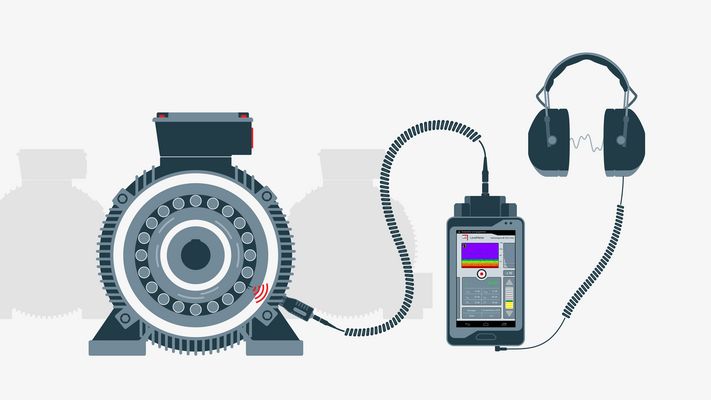
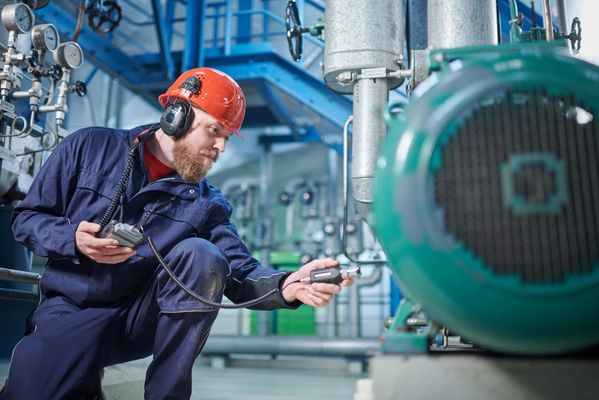
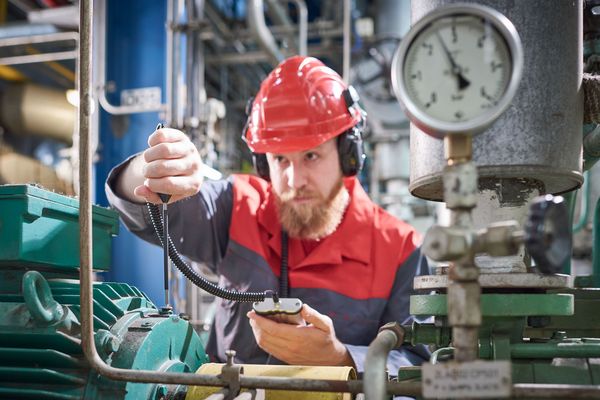
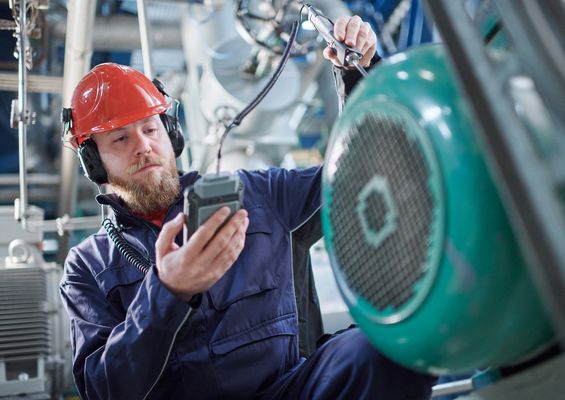
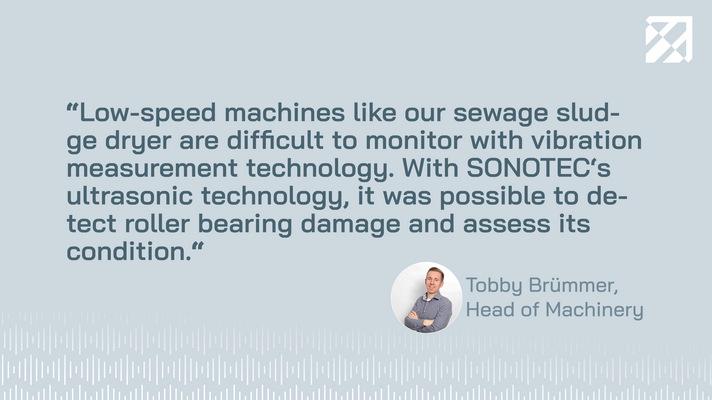
Products
One of the main reasons for bearing damage is insufficient lubrication, which leads to increased friction in the bearing. As a result, the acoustic emission increases. Under-lubrication, as well as potential over-lubrication, can be quickly detected with our ultrasonic inspection devices. Additionally, improper use, intrusion of foreign materials, and excessive heat generation are other reasons for damage to roller and ball bearings. These changes in condition can also be detected with ultrasound. Ultrasound helps to ensure that your bearings achieve their intended service life through proper monitoring and maintenance.
Ultrasound is the most suitable technology for this purpose
Ultrasound will enable you to detect damages at the earliest possible stage compared to other technologies. This is due to the fact that the acoustics in bearings are the first parameter which will change. Vibrations, noises that can be noticed by humans, and heat development only occur in advanced stages of damage. At this point, the bearing is already showing signs of damage and may need to be replaced quickly to avoid downtime.
Ultrasound offers a great advantage in that it can be used throughout all bearing rotational speeds. Even with extremely slow-running bearings, ultrasound has been able to help customers inspect their bearings and find faults in the earliest of stages.
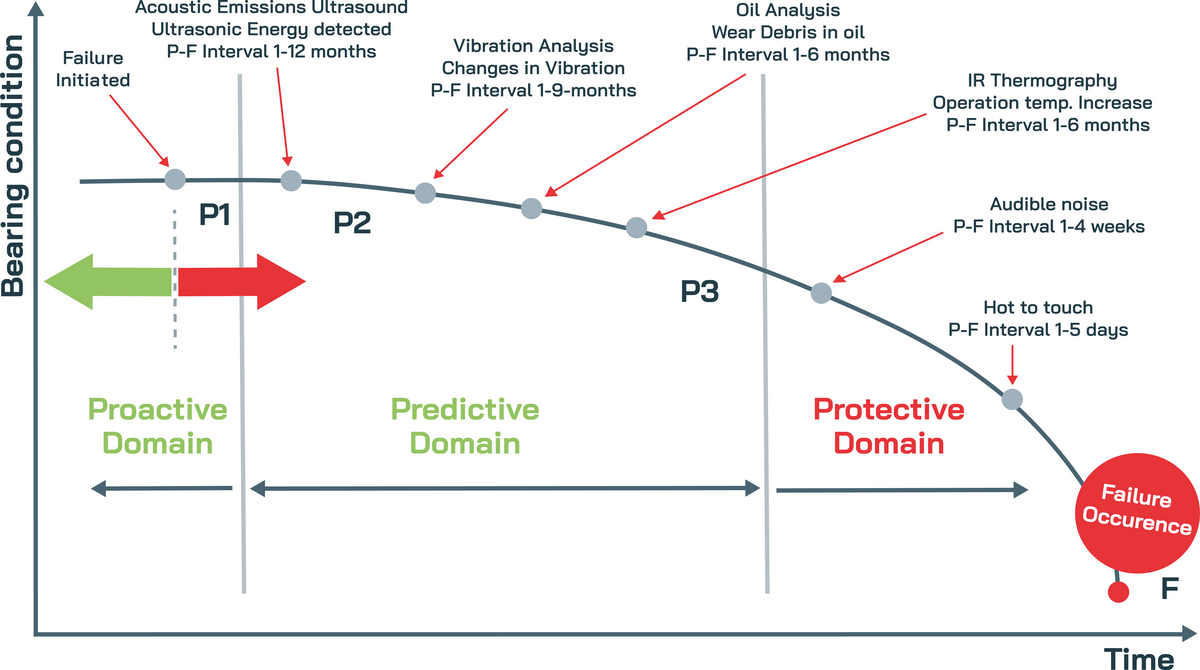
Our solution: A combination of broadband ultrasonic measuring device and asset tree management software
The combination of our powerful broadband ultrasonic device, intuitive apps, broadband sensor, and maintenance management software will help you achieve maximum efficiency in your ultrasonic condition monitoring program.
Customers are satisfied all over the world with our solution and we are firmly convinced that we can support you and your maintenance team in improving machine reliability in your plant.
With our ultrasonic testing devices developed and manufactured in Germany and the associated user-friendly software solutions, it is now possible optimize lubrication and to detect damage to bearings at an early stage.
See for yourself!
Success Story: SONOTEC X PD Energy GmbH · SONOTEC
Success Story: SONOTEC & University of Stuttgart · SONOTEC
Bearing Monitoring & Lubrication - Machine Testing with SONAPHONE
